The integration of their e-commerce and delivery management platforms has helped Chef’s Warehouse make light work of their order fulfilment process.
Chefs’ Warehouse prides itself as a one-stop shop for local cooking enthusiasts. It runs a culinary training school as well as a retail outlet that carries a comprehensive range of kitchen tools and ingredients.
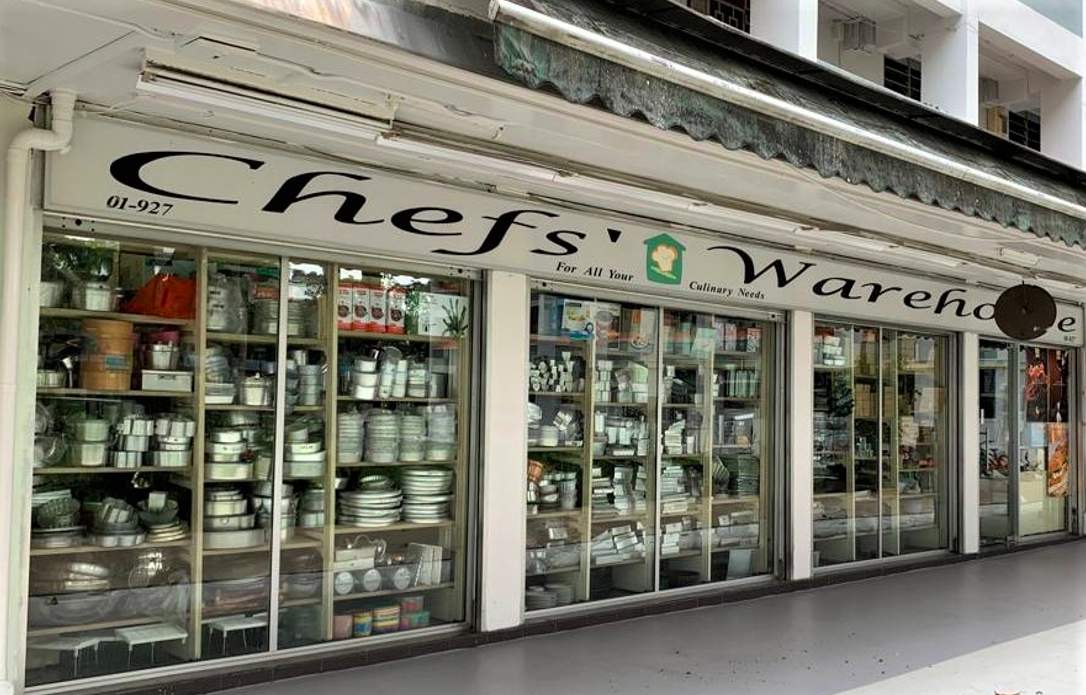
As an innovative small set-up, Chef’s Warehouse rode on the e-commerce wave and set up a simple e-store on its website for its retail business. However, the e-commerce shopfront was not integrated to a downstream delivery system. This meant that whenever online orders were made, the administrative worker had to manually note down the orders and re-enter them manually into a separate delivery order template. The orders are then passed physically to the retail assistant to process the deliveries before finally being dispatched to the end customers. With such a manual process, errors are inevitable, and they range from processing mistakes due to typographical error, miscommunication, or simply a loss of the physical ordering slips.
The manual scheduling and planning of routes was inefficient for both the administrative scheduler and the delivery drivers, as the routes often have to be amended based on subsequent new orders. At times, it even led to a mix up of deliveries which resulted in wasted trips and unhappy customers.
Manual recording and processing meant the drivers had to constantly make trips back to the main office. As customers confirm receipt of their goods via endorsement of hard copy delivery orders, the documents had to be sent back to the office for physical filing.
In order to improve the efficiency of its day-to-day processes, Chef’s Warehouse partnered with NTUC’s Employment and Employability Institute (e2i) through the WorkPro Job Redesign scheme to introduce an integrated delivery management system. The aim of the collaboration was to ensure the seamless transition of e-commerce orders from order fulfilment to last mile delivery, so that each step of the process is intuitive and efficient.
The key improvement with the integration of the e-commerce portal and the delivery management system is the elimination of manual data entry as the online orders can be processed for delivery immediately once payment has been made on the e-store.
With a single source of truth, all incremental updates to the data, for instance when delivery drivers pick up the items or when orders are delivered, is updated directly in the system without the need for manual documents. All reports are generated based on the same set of data, so the speed and reliability of the reports are improved.
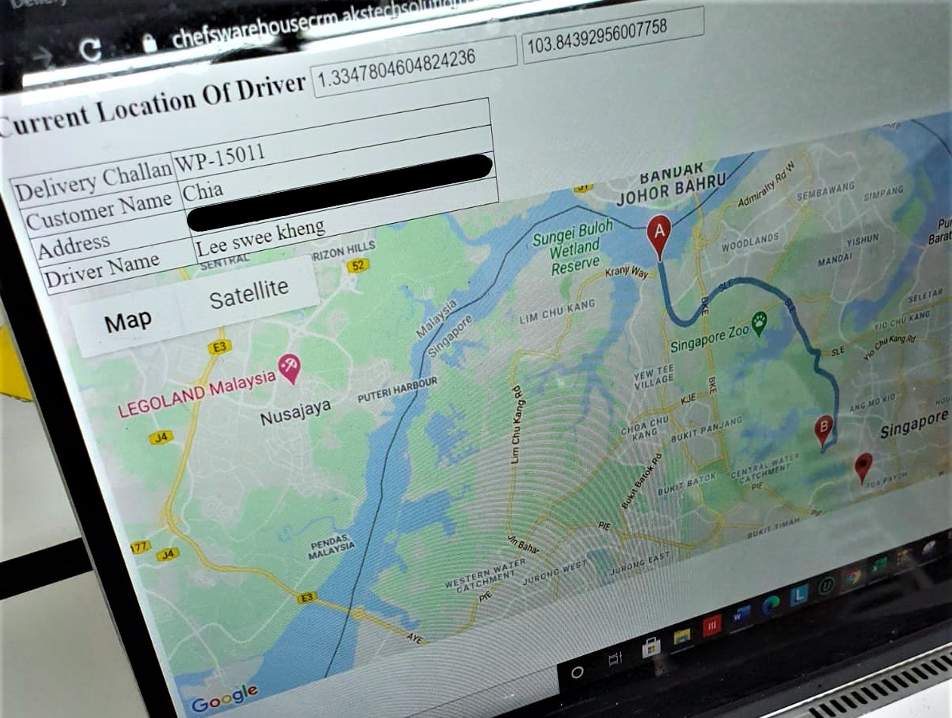
On a daily basis, the administrative worker is only required to trigger the ‘Smart Assign’ feature on the delivery management system, and all the pending tasks will be automatically assigned to all active delivery drivers based on the system embedded algorithm. This ensures that the most efficient delivery routes are planned, minimising the need for any detours.
As orders on the e-store flow instantly into the delivery management system, the Chef’s Warehouse team can view a full overview of the tasks assigned to its delivery team in real-time. The on-going status of delivery tasks can be tracked by the administrator as there is GPS location tracking of the delivery drivers. Whenever a delivery is completed, the status is instantaneously synchronised to the backend.
For each assigned trip, the delivery driver can simply click on the address of deliveries and the most efficient route will be planned for them automatically on the application. With the ability to track the real-time location of delivery drivers, the administrator will now be able to generate delivery tracking links to customers to allow them to track the estimated time of arrival.
Delivery drivers utilise their delivery mobile application to allow customers to sign off electronically as acknowledgment of goods receipt. The signed electronic delivery orders are captured automatically on the solution backend, so the delivery drivers no longer need to plan separate trips back to the main office to return physically signed delivery orders for administrative filing. With support for both Android and iOS, the older delivery workers even have flexibility in the choice of their mobile phones.
Despite maintaining the same headcount with the implementation of the delivery management system, the older workers in Chef’s Warehouse can now manage their daily tasks in an easier and smarter manner due to the streamlining of the end-to-end workflow. The company has shared the productivity gain with three of its older workers (aged 50 and above) through with a wage increment.
With a fully integrated solution powering its business, the Chef’s Warehouse team is now primed for growth through the support of e2i. The integrated workflow facilitates the efficient processing and dispatch of orders even with an increased volume.
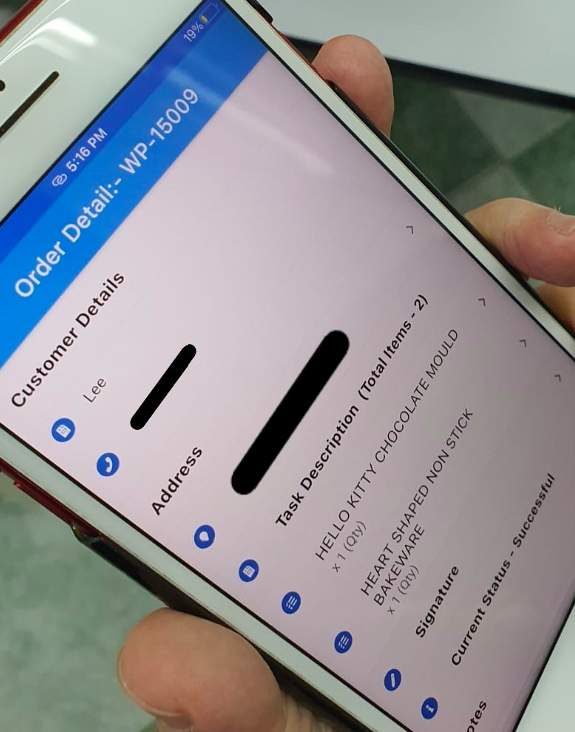